microchip公司的dsPIC33F系列是高性能16位数字信号控制器(DSC),接纳改进的哈佛架构,高达40MIPS,16位数据通路,24位指令,工作电压3.0-3.6V,主要用在各种马达控制如无刷DC马达,单相和三相马达与开关磁阻电动机。别的也可用在UPS,逆变器,开关电源,功率因素修正以及服务器,通信设备和其它工业设备的电源管理模块。本京电港论坛文章先容了dsPIC33F主要特点,方框架图以及Cerebot MC7马达控制板主要特点,方框架图和电路原理图纸。
The dsPIC33FJXXXMCX06A/X08A/X10A family of devices supports a variety of motor control applications, such as brushless DC motors, single and 3-phase induction motors and switched reluctance motors. The dsPIC33F Motor Control products are also well-suited for Uninterrupted Power Supply (UPS), inverters, Switched mode power supplies, power factor correction and also for controlling the power management module in servers, telecommunication equipment and other industrial equipment.
dsPIC33F主要特点:
Operating Range:
• Up to 40 MIPS operation (@ 3.0-3.6V):
- Industrial temperature range (-40 ℃ to +85℃)
- Extended temperature range (-40℃ to +125℃)
• Up to 20 MIPS operation (@ 3.0-3.6V):
- High temperature range (-40℃ to +150℃)
High-Performance DSC CPU:
• Modified Harvard architecture
• C compiler optimized instruction set
• 16-bit wide data path
• 24-bit wide instructions
• Linear program memory addressing up to 4M instruction words
• Linear data memory addressing up to 64 Kbytes
• 83 base instructions: mostly 1 word/1 cycle
• Two 40-bit accumulators:
- With rounding and saturation options
• Flexible and powerful addressing modes:
- Indirect, Modulo and Bit-Reversed
• Software stack
• 16 x 16 fractional/integer multiply operations
• 32/16 and 16/16 divide operations
• Single-cycle multiply and accumulate:
- Accumulator write back for DSP operations
- Dual data fetch
• Up to ±16-bit shifts for up to 40-bit data
Direct Memory Access (DMA):
• 8-channel hardware DMA
• 2 Kbytes dual ported DMA buffer area (DMA RAM) to store data transferred via DMA:
- Allows data transfer between RAM and a peripheral while CPU is executing code (no cycle stealing)
• Most peripherals support DMA
Interrupt Controller:
• 5-cycle latency
• Up to 67 available interrupt sources
• Up to five external interrupts
• Seven programmable priority levels
• Five processor exceptions
Digital I/O:
• Up to 85 programmable digital I/O pins
• Wake-up/Interrupt-on-Change on up to 24 pins
• Output pins can drive from 3.0V to 3.6V
• Up to 5.5V output with open drain configuration on 5V tolerant pins with an external pull-up
• 4 mA sink on all I/O pins
On-Chip Flash and SRAM:
• Flash program memory, up to 256 Kbytes
• Data SRAM, up to 30 Kbytes (includes 2 Kbytes of DMA RAM)
System Management:
• Flexible clock options:
- External, crystal, resonator, internal RC
- Fully integrated PLL
- Extremely low jitter PLL
• Power-up Timer
• Oscillator Start-up Timer/Stabilizer
• Watchdog Timer with its own RC oscillator
• Fail-Safe Clock Monitor (FSCM)
• Reset by multiple sources
Power Management:
• On-chip 2.5V voltage regulator
• Switch between clock sources in real time
• Idle, Sleep and Doze modes with fast wake-up
Timers/Capture/Compare/PWM:
• Timer/Counters, up to nine 16-bit timers:
- Can pair up to make four 32-bit timers
- 1 timer runs as Real-Time Clock (RTC) with external 32.768 kHz oscillator
- Programmable prescaler
• Input Capture (up to eight channels):
- Capture on up, down or both edges
- 16-bit capture input functions
- 4-deep FIFO on each capture
• Output Compare (up to eight channels):
- Single or Dual 16-bit Compare mode
- 16-bit Glitchless PWM mode
Communication Modules:
• 3-wire SPI (up to two modules):
- Framing supports I/O interface to simple codecs
- Supports 8-bit and 16-bit data
- Supports all serial clock formats and sampling modes
• I2C™ (up to 2 modules):
- Full Multi-Master Slave mode support
- 7-bit and 10-bit addressing
- Bus collision detection and arbitration
- Integrated signal conditioning
- Slave address masking
• UART (up to 2 modules):
- Interrupt on address bit detect
- Interrupt on UART error
- Wake-up on Start bit from Sleep mode
- 4-character TX and RX FIFO buffers
- LIN/J2602 support
- IrDA® encoding and decoding in hardware
- High-Speed Baud mode
- Hardware flow control with CTS and RTS
• Enhanced CAN (ECAN™ technology) 2.0B active (up to 2 modules):
- Up to 8 transmit and up to 32 receive buffers
- 16 receive filters and three masks
- Loopback, Listen Only and Listen All Messages modes for diagnostics and bus monitoring
- Wake-up on CAN message
- Automatic processing of Remote Transmission Requests
- FIFO mode using DMA
- DeviceNet™ addressing support
Motor Control Peripherals:
• Motor Control PWM (up to eight channels):
- Four duty cycle generators
- Independent or Complementary mode
- Programmable dead time and output polarity
- Edge or center-aligned
- Manual output override control
- Up to two Fault inputs
- Trigger for ADC conversions
- PWM frequency for 16-bit resolution (@ 40 MIPS) = 1220 Hz for Edge-Aligned mode, 610 Hz for Center-Aligned mode
- PWM frequency for 11-bit resolution (@ 40 MIPS) = 39.1 kHz for Edge-Aligned mode, 19.55 kHz for Center-Aligned mode
• Quadrature Encoder Interface (QEI) module:
- Phase A, Phase B and index pulse input
- 16-bit up/down position counter
- Count direction status
- Position Measurement (x2 and x4) mode
- Programmable digital noise filters on inputs
- Alternate 16-Bit Timer/Counter mode
- Interrupt on position counter rollover/underflow
Analog-to-Digital Converters (ADCs):
• Up to two ADC modules in a device
• 10-bit, 1.1 Msps or 12-bit, 500 Ksps conversion:
- Two, four or eight simultaneous samples
- Up to 32 input channels with auto-scanning
- Conversion start can be manual or synchronized with one of four trigger sources
- Conversion possible in Sleep mode
- ±1 LSb max integral nonlinearity
- ±1 LSb max differential nonlinearity
CMOS Flash Technology:
• Low-power, high-speed Flash technology
• Fully static design
• 3.3V (±10%) operating voltage
• Industrial and extended temperature
• Low-power consumption
Packaging:
• 100-pin TQFP (14x14x1 mm and 12x12x1 mm)
• 80-pin TQFP (12x12x1 mm)
• 64-pin TQFP (10x10x1 mm)
• 64-pin QFN (9x9x0.9 mm)
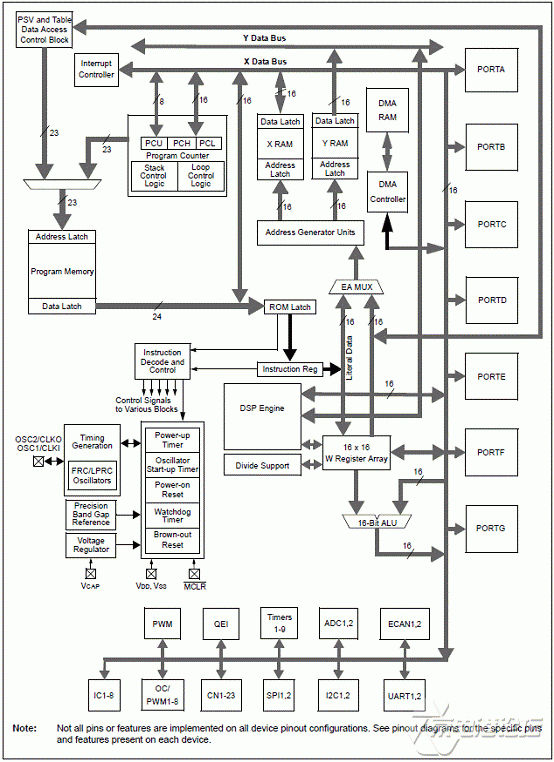
图1{京电港论坛}。dsPIC33F系列方框架图
Cerebot MC7马达控制板
The Cerebot MC7 board is microcontroller development board based on a Microchip dsPIC 16-bit Digital Signal Controller.
The Cerebot MC7 is primarily intended to be used as a controller for electro-mechanical devices such as DC motors. The microcontroller used, a dsPIC33FJ128MC706A, is a member of a dsPIC family optimized for motor control applications.
The Cerebot MC7 provides four Half-Bridge circuits that are rated for 24V at up to 5A. Each of these Half Bridge circuits is connected to the dsPIC A/D converter to measure voltage and current for closed loop feedback control. These half bridges can be used to control two brushed DC motors, two bi-polar stepper motors, one brushless DC motor, one uni-polar stepper motor. In addition, the board can be used to implement controllers for switched DCDC converters.
The Cerebot MC7 works with the Microchip MPLAB® development environment and provides built in programming and debugging support within the MPLAB® IDE.
Cerebot MC7马达控制板主要特点:
a dsPIC33FJ128MC706A microcontroller
four 24V/5A Half Bridge circuits with current and voltage feedback and provision for over-current interrupt
power supply voltage up to 24V
5V/4A switching power supply
integrated programming/debugging circuit
one CAN network interface
three Pmod connectors for Digilent peripheral module boards
eight RC servo connectors
two I2C daisy chain connectors
256Kbit I2C EEPROM
two push buttons and four LEDs
ESD protection and short circuit protection for all I/O pins.

图2{京电港论坛}。Cerebot MC7马达控制板外形实物图
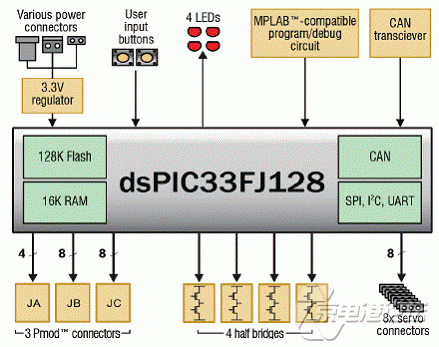
图3{京电港论坛}。Cerebot MC7马达控制板框架图
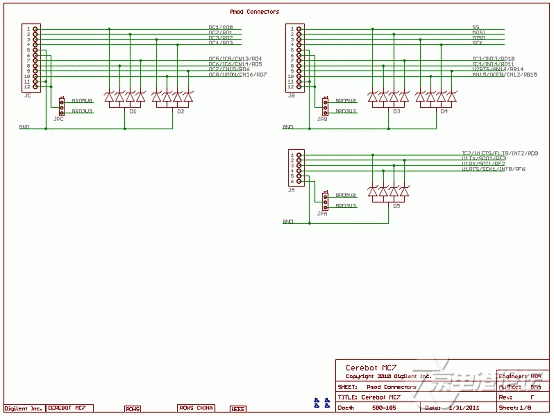
图4{京电港论坛}。Cerebot MC7马达控制板电路原理图纸(1)
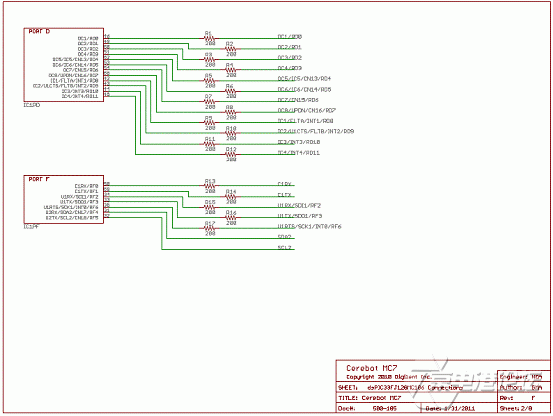
图5{京电港论坛}。Cerebot MC7马达控制板电路原理图纸(2)
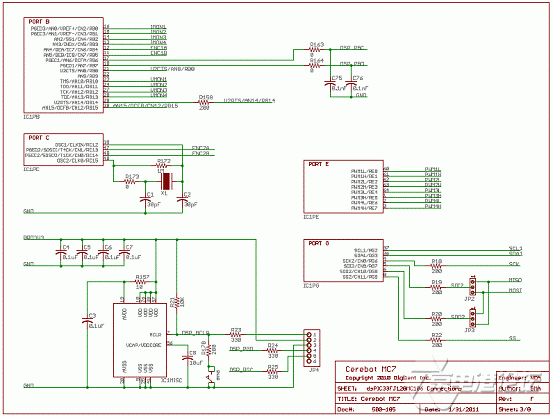
图6{京电港论坛}。Cerebot MC7马达控制板电路原理图纸(3)
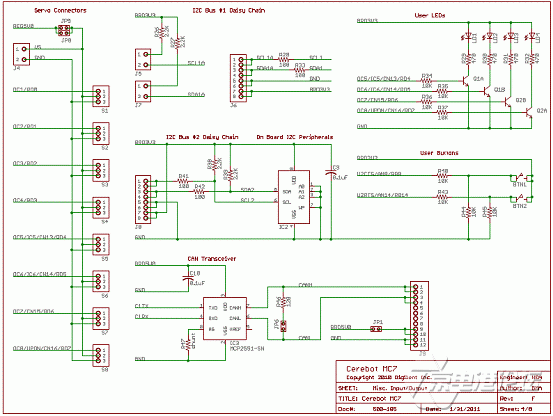
图7{京电港论坛}。Cerebot MC7马达控制板电路原理图纸(4)
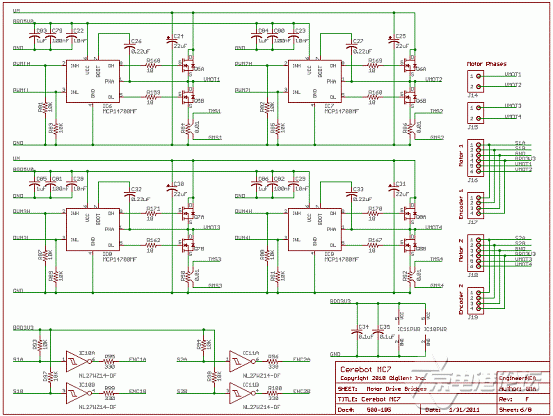
图8{京电港论坛}。Cerebot MC7马达控制板电路原理图纸(5)
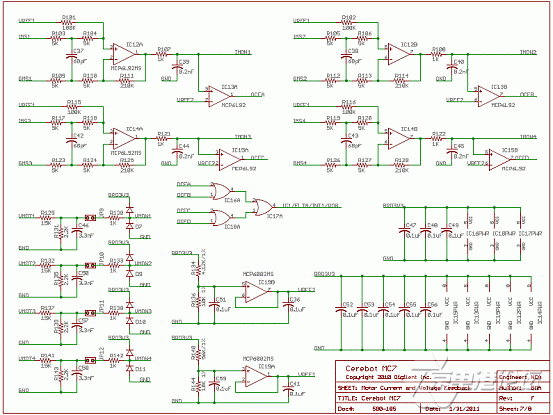
图9{京电港论坛}。Cerebot MC7马达控制板电路原理图纸(6)
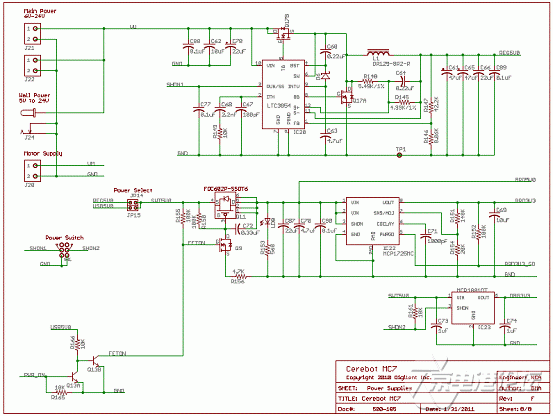
图1{京电港论坛}0。Cerebot MC7马达控制板电路原理图纸(7)
详情请复制打开此衔接地址:
http://ww1.microchip.com/downloads/en/DeviceDoc/70594C.pdf
和
http://www.digilentinc.com/Data/Products/CEREBOT-MC7/Cerebot%20MC7_sch.pdf